- Evaluating and improving the performance of individual stations, departments, orders, machines
- Meet the service level agreement (SLA) with your customers
- Digital and fast overview of the entire order status and progress
- Mastering shortage of skilled workers – with automation you can use your resources for really important and margin-generating tasks
Get a
digital overview
with Stations
Production tracking for your smart factory
Digital. Networked. Customized.
You already have your MIS, web shop, and large production machines networked. But what about the many additional activities, no matter how small? Do you get calls from customers asking when their order will be delivered?
With OneVision’s Stations, the entire production process can be digitally mapped and monitored. Manual activities in particular, such as manual work or machines without a digital interface, can be integrated directly into the workflow. Network analog punch presses, Heidelberg Tiegel, sewing departments, manual order picking and much more.
Employees can be guided by instructions or provided with information at the respective work steps. Feedback and status updates from the individual stations are displayed in the workflow and enable the production status to be tracked. For your smart factory.
The advantages of Stations
- Job overview enables quick tracking of orders
- Reduce walking distances/disruptions for employees to check the production status
- Evaluation of production for process optimization and error analysis
- Integration of analog machines: Heidelberg Tiegel, inserters, etc.
- Integration of manual activities: sewing, corner rounding, eyeletting, drilling, picking, etc.
- Integration of outcourced digital processes (e.g. without API-Interface)
- Acceleration of throughput times through process optimization
- Dashboard: Every station displayed, with indication of current backlog
- Evaluation and performance improvement of individual stations, departments, orders, machines
- Status updates for your MIS System
Complete digital transformation
Often, manual or analog production steps are required to meet individual customer needs.
With OneVision’s Stations, you can integrate any type of manual work step, as each individual station can be configured individually. This means you can digitally map all the stations you need and get order status at the touch of a button. You can see the stations, the pending orders and whether a user is logged in there.
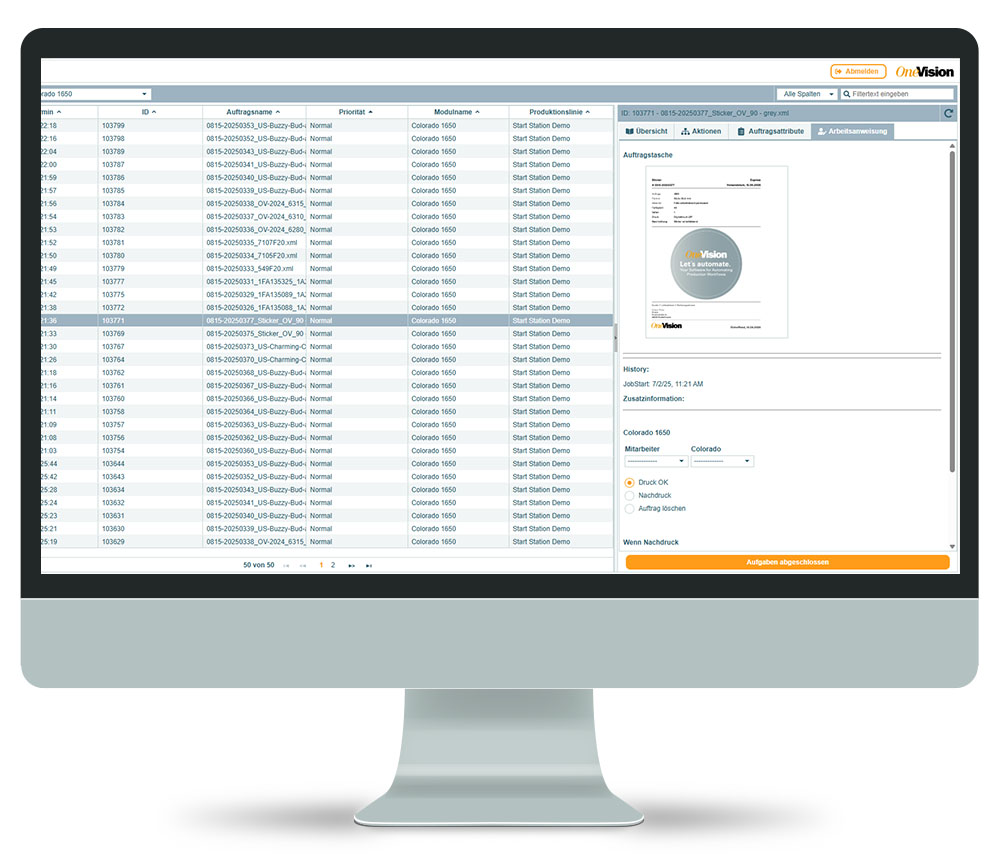
Stations in detail
Configure your desired stations (once) in the assembly line editor. You specify your individual parameters for each station and thus enable digital integration into your workflow. All pending orders are listed for the operator at the selected station. Barcodes or Job-IDs prevent mix-ups and ensure fast production.
However, there is always the option of manual interaction, e.g. to enter additional information. It is also possible to create individual buttons or drop-down menus to change order attributes and mark the order as "successfully processed" or "faulty, reprint required", for example. This allows you to bring faulty items back into the production process as quickly as possible, either as information to the person responsible or as a direct option to start a reprint.
Barcodes/QR-Codes
With Stations it is possible to give the system feedback via scanned barcodes/QR codes, e.g. scanning the status "ok".
How OneVision Stations benefits you as a...
Managing Director
Production Manager
- Digital mapping of all stations involved in the production process
- Real-time tracking of the production status of all orders
- Instruction of employees at the individual work steps reduces errors
- Quality control through inspection and feedback function
Workflow Manager
- Guided work steps through digital instructions
- Collection of all relevant information in a digital system
- Direct feedback function
- User-friendly interface
Stations comes with a mobile app for tablet and smartphone. This allows you to control and handle your jobs quickly and easily with your iOS or Android device.
- Transparent overview of all orders at a station
- Job selection via order ID or integrated barcode scanning
- Direct instructions and feedback function on the mobile device
- Built-in photo function for quality control and documentation