Your press contact at OneVision
+49 (0)941 78004-456
marketing[at]onevision.com
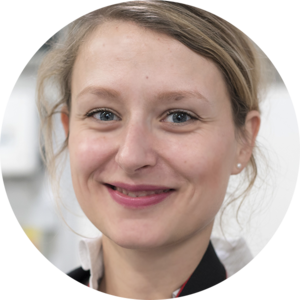
Karin Bader, Marketing OneVision Software“I look forward to hearing from you if you have any questions about press releases, newsletters, and more.”
Your press contact at OneVision
+49 (0)941 78004-456
marketing[at]onevision.com
Karin Bader, Marketing OneVision Software“I look forward to hearing from you if you have any questions about press releases, newsletters, and more.”