Your start
to automation
The road to print workflow automation
What will be automated?
In order to automate workflows in print production the existing processes must first be identified and then improved. With the right software in place, the next step is their automation. These steps are taken by our workflow consultants together with the respective print shop. The actual and target processes are visualized, for example with the help of mind maps.
Assessing the status quo
The starting point is a comprehensive analysis of the process landscape. For each print product, the workflow consultant records the route from incoming orders through data preparation (prepress) to printing, finishing and logistics. A prerequisite for automation is the correct recording and documentation of current processes. The individual process steps are examined from different perspectives. It is very important that the workflow consultant talks to both, those involved in the process and those responsible for the product or production. The active collaboration of the print shop's production managers is immensely important.
The inventory is accomplished, the identified processes are being presented including detected deficiencies and weaknesses as well as "low hanging fruits", i.e. processes that can be optimized with relatively little effort:
- analyze existing processes
- ”low hanging fruits”
- select suitable product/workflow
- identify redundant activities
Defining target processes
Often processes haven’t changed in years because "never change a running system". Even when production conditions change (new machines, new software, new products), familiar routines are often retained. It makes little sense to automate these non-optimal processes.
This step determines the scope of process automation. Processes can be automated as they were identified during the inventory analysis. Or – as can be seen in the picture – the process landscape is completely revised depending on the goals and strategy of the company.
Automation expert OneVision
Our automation solutions are not off-the-shelf – after all, neither are your requirements. That is why we first define together with you which processes are already in place, where there is a need for optimization and how new processes can be implemented with OneVision software solutions.
Document optimized processes
The optimized processes are now being documented. This seems trivial, but it’s essential. Because without documentation of the jointly developed, improved processes, different memories will quarrel about the details after a short time. Conscientious documentation, signed by all parties involved, ensures that there is agreement on the goal. Everyone is on the same page.
Choose automation software
Now that the processes to be automated are known, you can search for the best and most suitable software. From my point of view, the OneVision software is the best choice for this task in most cases. It is flexible, can be adapted to different requirements and customers have direct contact persons they can reach out to directly in case of questions.
Achieve a common level of understanding
Automation and the road to automation must be discussed openly and in detail with both, management and staff. Changing processes means changing habits. Some employees are more willing than others to adapt. It certainly helps to get the hesitators on board as early as possible. This can be done best through success. Time for quick wins: What is needed are processes that can be easily and quickly automated or that offer an obvious and major advantage over the previous procedure. These processes are the ones to automate first. If the new process leads to fewer errors, faster production and/or lower costs after a very short time, then there is little reason to block the process.
Digitize and automate improved processes
Start with a process, a print product. Map the agreed process with the help of the chosen automation software. Then test the result. It may be necessary to re-adjust the settings.When you are satisfied and the employees are used to the new process, it is time to automate the next process.
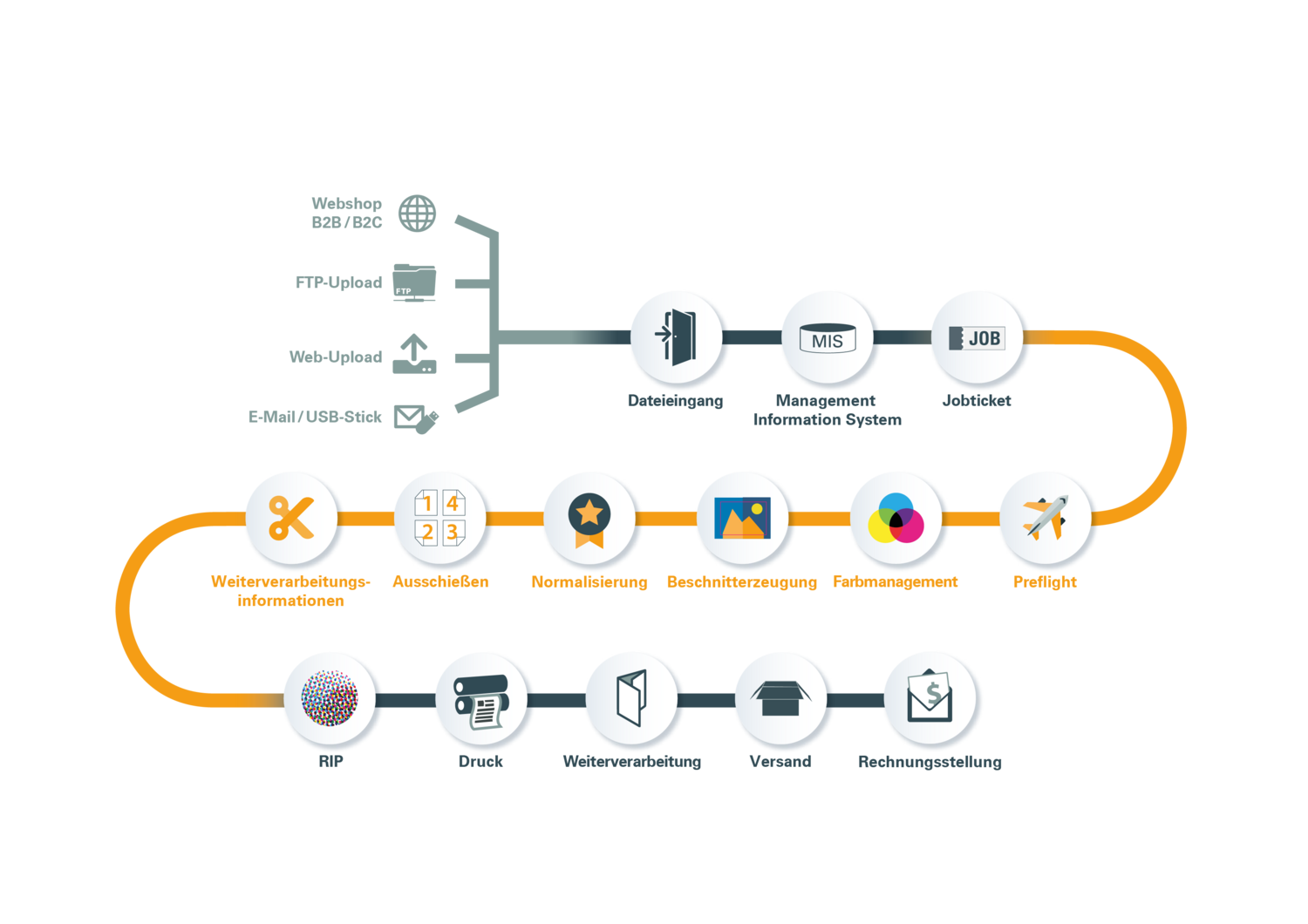
DIY or consultants?
Our recommendation is to get help from outside. Each of the above steps are more effective, when experts lead the process. The assessment will be more accurate because external experts examine the process impartially. Having experience with print production processes in other companies, experts can provide good assistance in defining and documenting new, improved processes. Experts know professional software that helps to automate the defined processes in the best possible way. Of course, external consultants cost money, but the benefits in terms of both quality and speed of process optimization are very high. It pays off in the end.
Start now with your individual print workflow automation!